News and Notes
Catch up on the latest
Take a moment and read the latest stories about people who use our products, events Ottobock attends and organizations that are doing good work. Feel free to share a particularly interesting tidbit with friends and family, too. And, if you have something to share, please send it to us.
11/11/19
First patient in North America fit with Ottobock’s FDA-cleared Myo Plus pattern recognition system
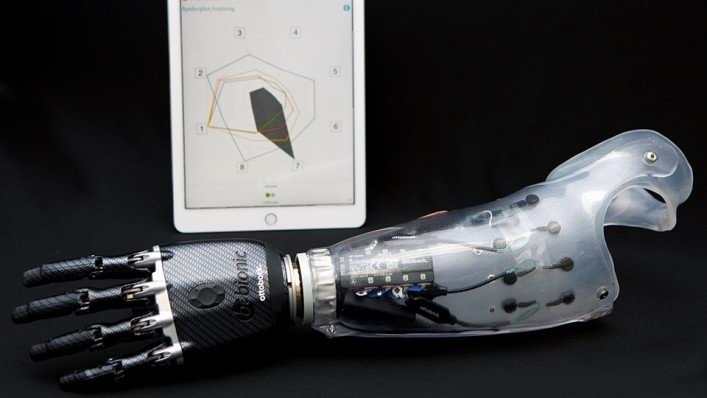
AUSTIN, TEXAS (November 11, 2019) - Ottobock is excited to announce its newest advancement in upper-limb prosthetics, the Myo Plus pattern recognition system. Pattern recognition represents a new paradigm in the control of a myoelectric prosthesis. On October 29, 2019 Ottobock partnered with Hanger Clinic to fit the first person in North America with a transradial upper limb amputation with the newly FDA-cleared technology.
Traditionally, individuals with transradial upper limb amputation have been fit with myoelectric hands controlled by electromyographic (EMG) signals. The conventional transradial myoelectric prosthesis is designed with one or two electrodes that transmit the EMG signals produced by the flexor and extensor muscles in the residual limb. Some users have found these systems difficult to learn due to complex switching mechanisms required to change between the hand, wrist, or multiple grip patterns a hand may offer. In some cases, this difficulty may lead to poor adoption or even abandonment of the prosthesis.
Uniting artificial intelligence with the intuitive and innate EMG signals of the user, Myo Plus adapts to their natural movements versus requiring the user to adapt to the system. While standard myoelectric systems are limited to sensing only two muscle signals, Myo Plus employs up to 18 sensors, enabling multiple muscle signals to be captured as unique movement patterns, each individually assigned to control various functions of the prosthesis. For example, one pattern is used to open the hand, another to close it, a third pattern to rotate the wrist moving the palm of the hand up, and a fourth to rotate the wrist moving the palm of the hand down. Offering direct, convenient control of the prosthesis without any switching mechanisms required and the ability to fine-tune adjustments via an app, the Myo Plus system was designed with both the user and prosthetist in mind.
Chris Lake, L/CPO, FAAOP, an upper limb specialist with Hanger Clinic, fit the first North American patient, Mark Kirby, with the Myo Plus system in Hurst, Texas. Lake said, “Pattern recognition offers an alternative for patients who may not be a candidate for more traditional myoelectric prostheses, or do not possess the muscle capacity to operate the prosthesis in a meaningful way. To a certain extent, standard myoelectric systems require significant muscular acrobatics to fully operate a prosthesis. From an energy expenditure standpoint, pattern recognition means not burning as much physical or mental energy thus providing the patient with prosthetic function that is more intuitive and less taxing."
Kirby, who has used a standard two-site myoelectric prosthesis for more than ten years said, “I loved the graphic representation of what was possible. I instantly saw how I could make the prosthetic wrist rotate versus opening and closing the prosthetic hand. It took away the mystery. Since it's more accurate, I'm less frustrated because I've got less accidental movements. Before, I had to really concentrate on my finger muscles. Now I can feel them again. I'm feeling muscles I haven't felt in years."
The relationship between the clinician and patient was an important consideration in the design of the Myo Plus pattern recognition system. The patented Spider Plot feature, a graphic representation of muscle patterns, is one of the system’s most unique and valued features. Via the Myo Plus app, the patient and practitioner can watch live as the muscle patterns are displayed on a graph shaped like a spider web. This visual feedback was designed to make the programming process simple and interactive for both the patient and prosthetist.
"The visual nature of the Spider Plot feature in Myo Plus makes it intuitive for Mark to learn how to use the technology, as well as understand the very finite changes he’s making as he contracts his muscles. It provides an instant connection between his muscles and his phantom hand,” said Lake.
If you would like additional information on the Myo Plus pattern recognition system, please contact Ottobock North America at 800 328 4058 or https://shop.ottobock.us/Contact.
About Ottobock
For 100 years Ottobock, the German global technology leader, has been developing med-tech products and fitting solutions for people with limited mobility in the areas of Prosthetics, Orthotics and Human Mobility. The company’s international activities are coordinated from the head office in Duderstadt/Germany. Ottobock has been investing, employing, researching and developing in the US since 1958 for the benefit of people with impaired mobility. Subsidiaries in 58 countries offer “Made by Ottobock” quality worldwide and employ more than 7,000 people.
Media Contacts
Cali Solorio│Ottobock North America│ 512 806 2655 │ Cali.Solorio@ottobock.com